DTP® Process
The DTP® Process is a high-yield propylene production technology in which propylene is produced by using dimethyl ether (DME) or methanol produced from natural gas, biomass, plastic wastes or other wastes via synthesis gas or mixed gas of green hydrogen and CO2 as a process feed. In addition, unavailable olefins by-produced from a naphtha cracker also can be used as process feed. The world demand for propylene is expected to increase steadily in the future, but the present supplies of propylene are seen as inadequate to meet this increased demand. In addition, the diversification of feedstock is needed as crude oil prices have soared. With this background, the attention of the propylene industry has become focused on the diversification of feedstock and propylene production processes intended for "on purpose" propylene production. JGC and Mitsubishi Chemical have jointly developed the DTP® process as a new propylene production technology. A demonstration test has been successfully completed through the operation of a demonstration plant constructed in Mitsubishi Chemical's Mizushima Plant. The DTP® Process is now ready for license.
Process Flow for Methanol Feedstock
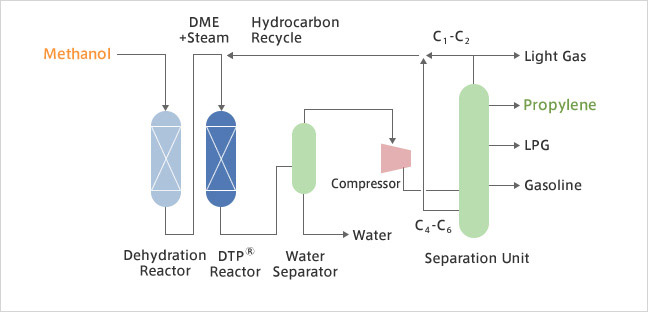
Features
- A DTP® catalyst (zeolite type) ensures high propylene selectivity and stable performance.
- A fixed-bed adiabatic reactor is adopted as a DTP® reactor. The reactor is easy to operate.
- A high propylene yield is attained by hydrocarbon recycling.
Applications
- Propylene production via methanol from natural gas in gas-producing countries
- Propylene production from methanol produced from biomass, plastic wastes or other wastes via synthesis gas or a mixture of green hydrogen and CO2
- Propylene production with the use of both fuel grade DME or methanol and unavailable olefins by-produced from a naphtha cracker
Keywords
- Methanol to propylene (MTP)
- Methanol to olefin (MTO)
Energy Transition - Gas/Oil/Chemicals
- The World's Most Advanced Energy-saving Condensate Desulfurization Process(JUSTTM Condensate)
- Integrated Hydrogen Desulfurization System - JUST® Refinery -
- Gas Oil Ultra-Deep Desulfurization Process
- Dimethyl Ether (DME) Synthesis Process
- High-Purity Hydrogen Sulfide Production Process
- DTP® Process
- Advanced Dehydration Process for Organic Compounds (Vapor-Phase PSA System)
- High-Throughput and High-Efficiency Extraction Column (WINTRAY®)