Producing environmentally beneficial products in volume and pioneering environmental technology business
Efforts towards Accomplishing Carbon Recycling
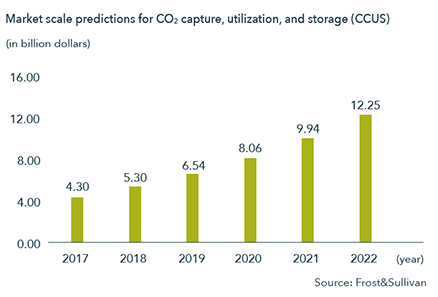
In order to substantially reduce carbon dioxide (CO2) output resulting from the use of fossil fuels in accordance with the 2℃ scenario established in the 2016 Paris Agreement, we must pursue all technological options.
JGC is promoting proactive efforts in various fields of research and development to limit the CO2 output resulting from fossil fuel use and to sequester carbon or accomplish effective carbon recycling.
JGC Initiatives to Accomplish Carbon Recycling
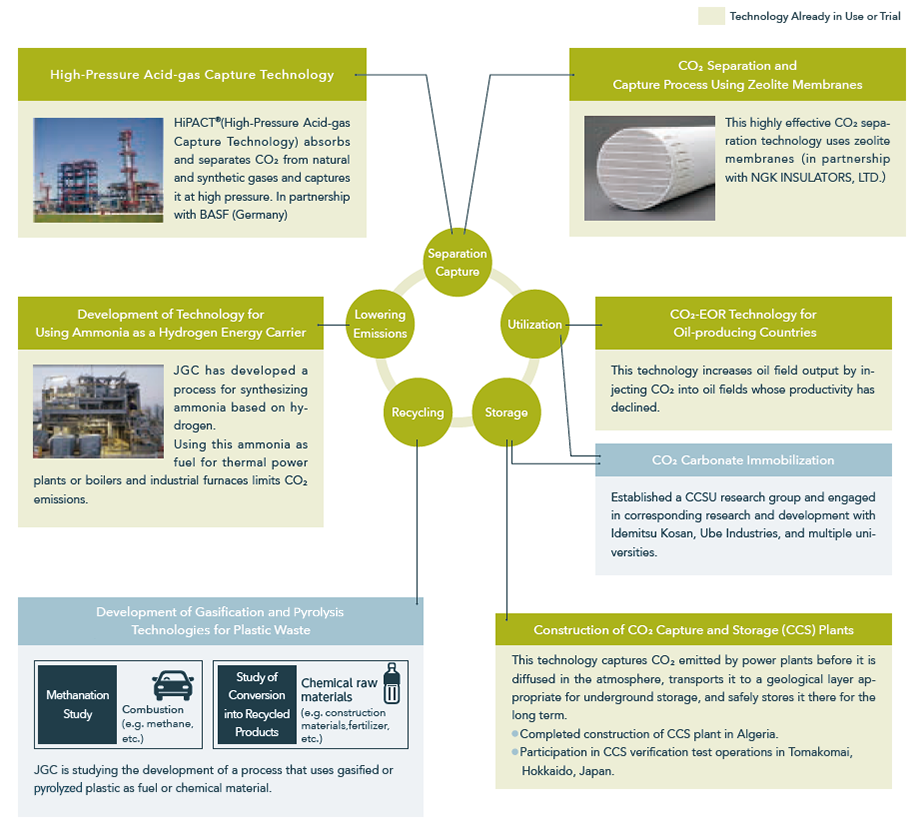
Recycling of Plastic and Fiber Waste
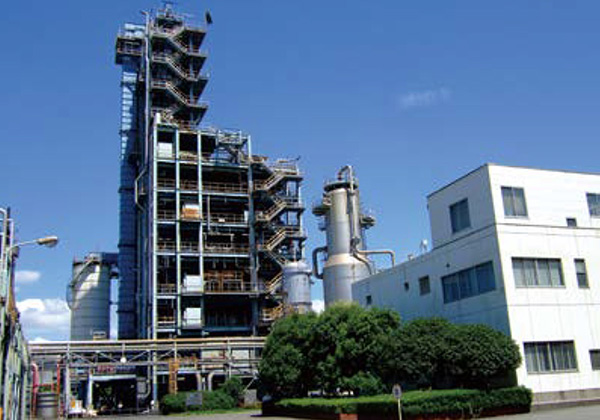
The JGC Group is participating in a pilot project in Saudi Arabia aimed at establishing a "blue" ammonia supply network to Japan, as promoted by the Institute of Energy Economics of Japan and Saudi Aramco, to promote wider adoption. For "green" ammonia, the JGC Group and Japan's National Institute of Advanced Industrial Science and Technology (AIST) collaboration successfully produced hydrogen from solar-powered water electrolysis, synthesized ammonia at low temperature and pressure, and generated 47 kW from an ammonia gas turbine in a world-first demonstration of a value chain. This early involvement in the market is valuable preparation not only for EPC but also licensing. Widespread adoption of ammonia as an energy carrier will also require larger production facilities. More recently, as part of a Green Innovation Fund project of Japan's New Energy and Industrial Technology Development Organization (NEDO), a pilot chemical plant jointly operated with Asahi Kasei Corp. has begun synthesizing "green" ammonia and other chemicals using a large-scale hydrogen production system. Efforts toward commercial applications on this large scale are accelerating.
Carbon Dioxide Capture and Storage (CCS) Technology
High-pressure Regenerative CO2 Capture (HiPACT®) Process
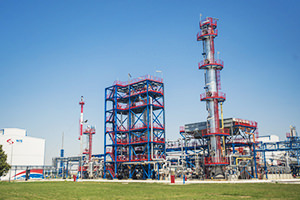
(operated by Naftna Industrija Srbije (NIS), Serbia)
HiPACT® is a technology for absorbing and separating CO2 from natural and synthetic gases and capturing it at high pressure. With this technology, CO2 can be stored underground (CCS: Carbon dioxide Capture and Storage) at low cost, while dramatically reducing additional energy required for CCS, helping to prevent global warming. The process, which was developed jointly by JGC and BASF, was introduced at a natural gas plant owned by INPEX Corporation in 2010 to demonstrate its viability. Since January 2015, a Serbian oil company has operated a commercial gas processing and CCS facility with a CO2 recovery unit using the HiPACT® process.
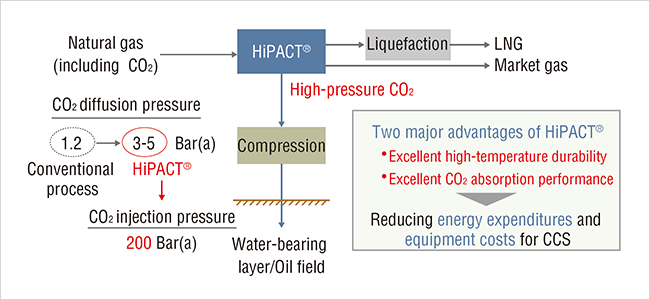
CCS Schematic
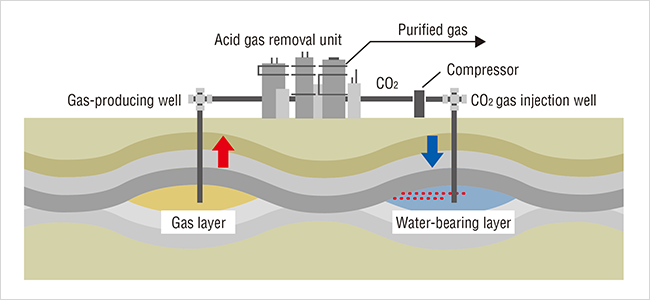
Using Ammonia as a Hydrogen Energy Carrier
There are high expectations surrounding the use of hydrogen, which does not emit CO2 during combustion, in addressing energy diversification and a low-carbon society, both of which are global challenges. However, due to many issues regarding both cost and safety involved in transporting and storing gaseous hydrogen, it must be converted into an energy carrier such as ammonia, liquefied hydrogen, or organic hydride to facilitate use.
Ammonia generates power through direct combustion and emits no CO2during the process because of its hydrogen and nitrogen composition. Also, infrastructure related to the transportation and storage of ammonia already exists. For those reasons, we are focusing on ammonia as a hydrogen energy carrier and are working to develop related technologies.
Development of a new process for ammonia synthesis using hydrogen as a raw material
The current issue with ammonia synthesis is the large volume of CO2emissions from the process of producing hydrogen using natural gas as raw material.
In order to reduce the CO2 generated in conventional synthesis, the development of hydrogen production methods involving electrolysis of water using renewable energy has been anticipated. However, energy efficiency has remained an issue due to pressurization of hydrogen for conventional ammonia synthesis, which is a necessary process as synthesis using renewable energy generates hydrogen at low pressure. In response to this issue, the company has developed a new catalyst for ammonia synthesis using low pressure hydrogen, and constructed a demonstration plant for producing ammonia at lower temperatures and pressures than conventional methods, using this catalyst. Going forward, we aim to establish hydrogen power generation technologies using ammonia as a fuel, and to conduct research on the further development of these technologies aimed at commercialization.
Widespread adoption of ammonia as an energy carrier will also require larger production facilities. More recently, as part of a Green Innovation Fund project of Japan's New Energy and Industrial Technology Development Organization (NEDO), a pilot chemical plant jointly operated with Asahi Kasei Corp. has begun synthesizing "green" ammonia and other chemicals using a large-scale hydrogen production system. Efforts toward commercial applications on this large scale are accelerating.

Sustainable Aviation Fuel
Also under review by the JGC Group is the establishment of a domestic value chain for A joint proposal with Revo International Inc. and Cosmo Oil Co. Ltd. on establishing a supply chain model for bio-jet fuel production from domestic used cooking oil was selected in a NEDO public call for proposals. The project is intended to develop and demonstrate a smart IT system for collecting used cooking oil, with Odakyu Electric Railway Co. Ltd., contracted by JGC Holdings. It will further accelerate business development toward the establishment of an SAF supply chain in the future.
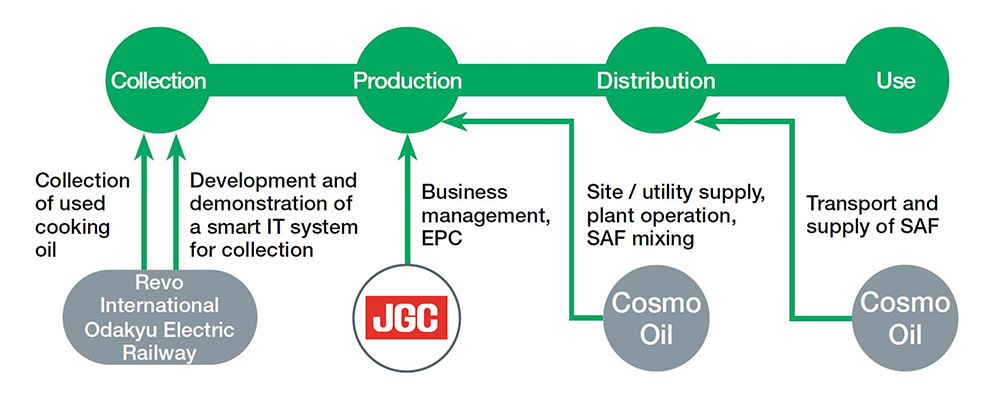
Production of Microbead Alternatives
Recent years have seen the global emergence of problems with essentially non-biodegradable microbead pollution in the ocean. Cosmetics manufacturers are now using less of the plastic beads, spurred in part by an EU policy introduced in early 2019 to phase out this material as an additive in various products.
As an alternative to plastic microbeads on a scale of hundreds of microns, which are used in cosmetics such as foundation, lipstick, emulsion, and sunscreen as well as abrasive products including face scrubs and toothpaste, JGC Group develops and sells beads of silicon dioxide (silica), an abundant natural resource that makes up nearly 60% of the Earth's crust. Silica is a naturally circulating, sustainable mineral component. Hydrophilic silica dissolves in water and is incorporated into phytoplankton and other organisms.
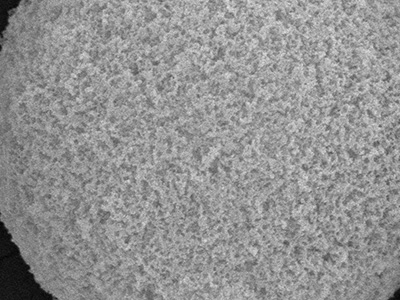
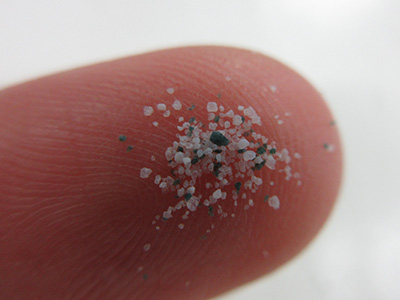
Volume Production of High Thermal Conductivity Substrates for EV/HEV Power Semiconductors
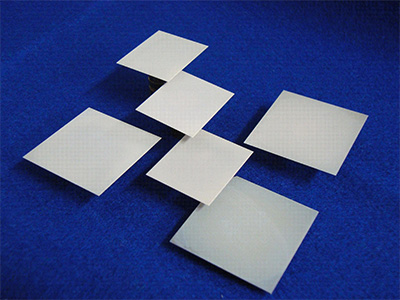
Amid growing needs for energy-efficient electric and hybrid vehicles, highspeed railways, and industrial equipment supporting a low-carbon society, it is essential to improve the performance of power modules that control the power of various equipment. Semiconductor substrates in particular are central in power modules, and as vehicle performance has improved in recent years, needs have emerged to develop robust components that do not break even under large currents.
By employing silicon nitride, a highly heat-resistant compound used in applications such as ball bearings, JGC Group has succeeded in developing silicon nitride ceramics with the world's highest thermal conductivity. Substrates made with the material withstand current 10 times higher than usual, which in conjunction with structural refinements that dissipate heat well can improve motor operating efficiency. Slated for operation in 2020, a plant to produce silicon nitride ceramic substrates in volume is now under construction.