Quality Management System
Basic Stance
Quality management is essential for safe operation and stable production at plants and other facilities. Under the ISO 9001-certified quality management system in place at the JGC Group, quality policies established by each company form the basis for quality targets set at various organizational levels. After organizational issues are identified, quality targets and action plans are formulated, implemented, evaluated, and improved in PDCA cycles for continuous improvement of organizational performance. Each company of the JGC Group ensures quality through systems and human resources that bring together valuable knowledge and skills built up over many years.
Quality management system
Under the ISO 9001-certified quality management system in place at the JGC Group, quality policies established by each company form the basis for quality targets set at various organizational levels. After organizational issues are identified, quality targets and action plans are formulated, implemented, evaluated, and improved in PDCA cycles for continuous improvement of organizational performance.
Framework for quality management at Group companies
Quality assurance committees or similar bodies are established at each Group company, and meet regularly.
The committees implement continuous improvements to ensure that quality of the products and services provided remains satisfactory, which includes investigating the root causes of any quality issues and preventing recurrence. The committees also evaluate these measures, as ongoing improvements are made.
In maintaining this framework for quality assurance, quality management activities are reviewed annually by the president of each company.
Quality management framework at each company
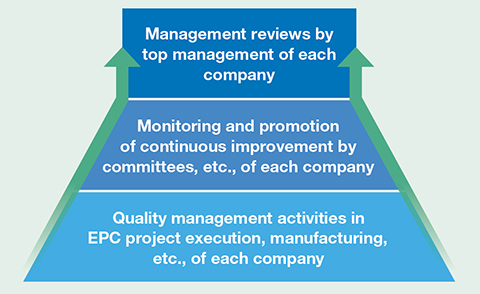
Lessons Learned—Leveraging valuable knowledge built up over the years
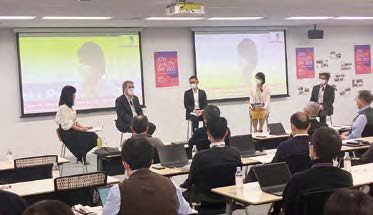
The JGC Group continually adopts ideas and initiatives for leveraging the knowledge and experience gained from past successes or failures (LL: Lessons Learned) to new projects.
The overseas EPC operating company JGC Corporation has developed the Corporate Lessons Learned (CLL) framework based on the lessons garnered from past projects, and provides it company-wide as a means of preventing severe quality problems.
All employees are given the opportunity to learn more using CLL, and the CLL courses in particular have been taken by a total of more than 11,000 employees including overseas group companies—all employees are united in our commitment to raising awareness of prevent quality problems from occurring. TQI (Think Quality Initiative) activities that forge a culture where everyone works to increase quality, are part of initiatives aimed at increasing quality performance, and include an annual Quality Day where employees have the opportunity to get together to openly discuss ideas that can help improve quality beyond existing frameworks.
The domestic EPC operating company JGC Japan Corporation holds a general operational meeting attended by executive level personnel, which includes a session called LL Discussion that covers past examples and ways to prevent problems with defects in the future. LL Communication shares details of defects to all employees across the organization, as part of ongoing efforts to raise awareness of quality.
Think Quality Initiative (TQI)
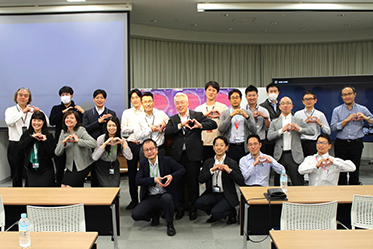
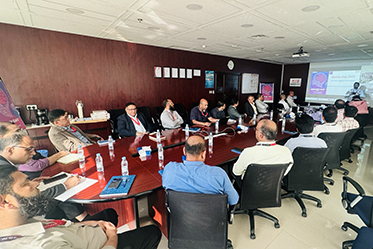
JGC Corporation, an overseas EPC operating company, carries out activities under the Think Quality Initiative (TQI) aimed at fostering a culture of permanent quality improvements and creating opportunities for ongoing dialogues on quality. The Group aims to strengthen unity with overseas Group companies and promote business execution through an integrated management system that includes Group-wide quality management. TQI is an important cross-group activity from the perspective of enhancing quality awareness. As part of these activities, every year the Group host a Quality Day to which the Group invite stakeholders from our overseas Group companies.
In fiscal 2023, Quality Day was held in November at the Yokohama Head Office, with approximately 800 people including employees from seven overseas Group companies participating in person and online. Following an opening speech by the President of JGC Corporation, there were video messages from construction sites, a panel discussion, and a “Quality Senryu” contest. During the panel discussion, each overseas Group company raised topics related to quality. Active discussions were held online on these topics between Head Office staff and representatives of overseas Group companies, thereby enhancing quality awareness.
For fiscal 2024, the domestic operating company JGC Japan Corporation will also participate in actively developing TQI activities.