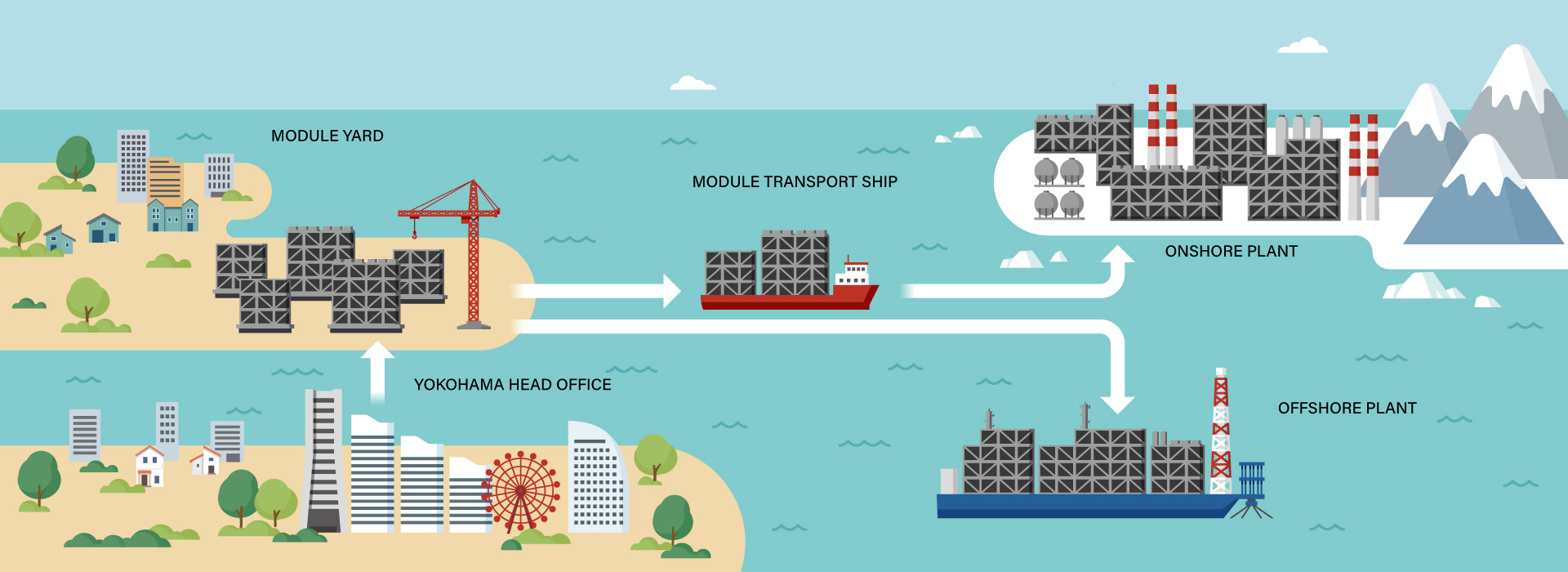
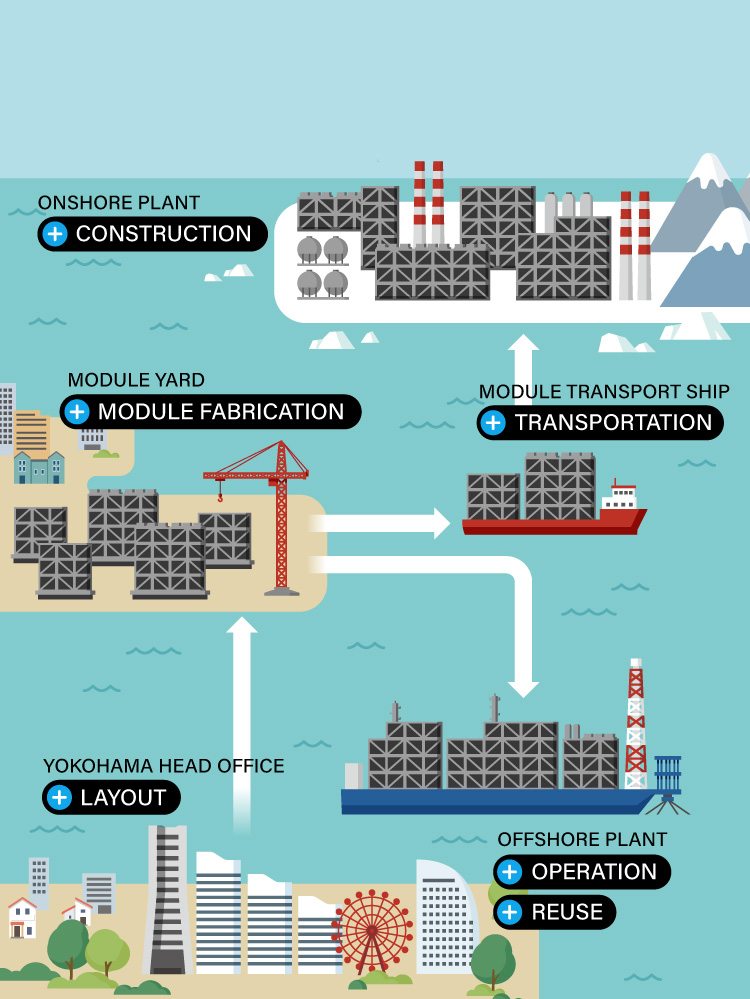
JGC GROUP'S MODULAR
CONSTRUCTION METHOD
With our advanced technical capabilities, we deliver safe, high-quality construction.
We use a technology called the Single Weld Hookup, which precisely aligns multiple modules and directly connects the ends of the piping.
The piping components will expand and contract during the transportation due to the differences in temperature between the module yard, and the plant construction site after transport. The amount of expansion and contraction is calculated in advance, and the module installation position is adjusted precisely.
Single Weld Hookup is characterized by our unique simulation method, which can accurately calculate the positional relationship between the ends of the piping when installing the module.
With conventional technology, a single pipe is inserted between the two module pipes and the end of module pipes and the single pipe are welded to the end of the connecting pipe, so two welds are required.
The application of Single Weld Hookup allows the piping at the module joints to be welded directly, reducing the number of welding points.
- Hydrogen and Ammonia
- Oil and Gas
- Chemicals
- Infrastructure
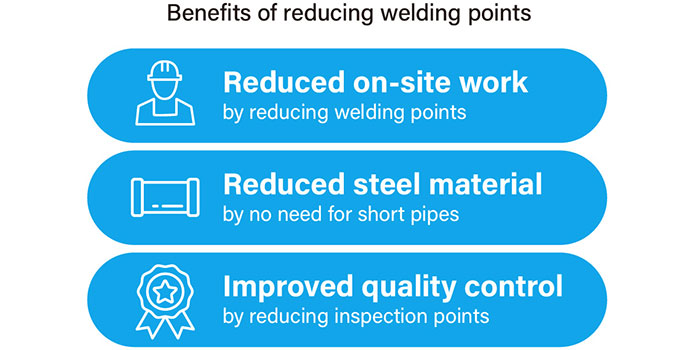
Transporting modules is characterized by the fact that there are more things to coordinate and more restrictions than when transporting the components of a plant, such as equipment and piping, directly to the construction site. Therefore, arranging module transport ships that match the schedule and selecting the transport route are the key.
Our group has a wealth of experience in transporting large modules for large-scale projects and transporting modules along the Northern Sea Route. In particular, we have expertise in sea ice forecasting and situation monitoring to reduce the risk of ice accretion on ships and cargo in cold regions.
- Nuclear power
- Hydrogen and Ammonia
- Oil and Gas
- Renewable energy
- Infrastructure
- Chemicals
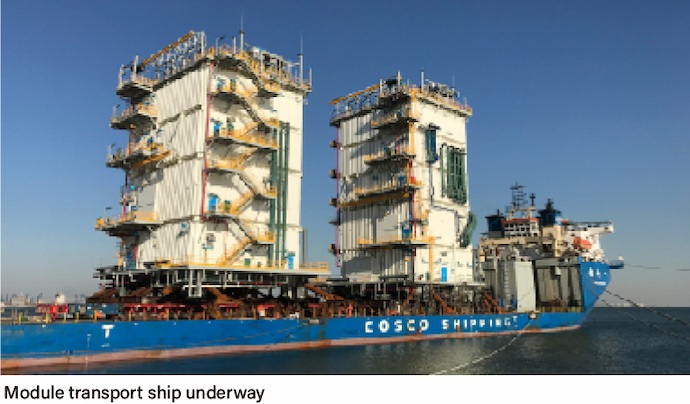
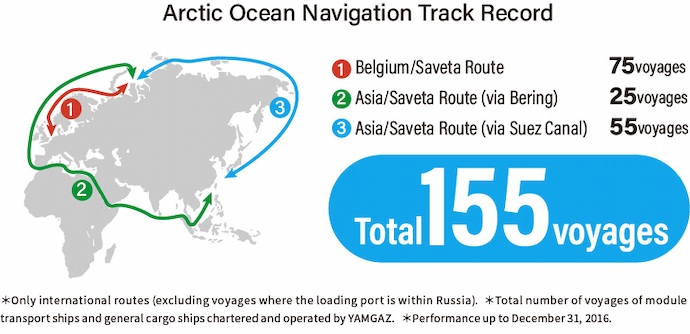
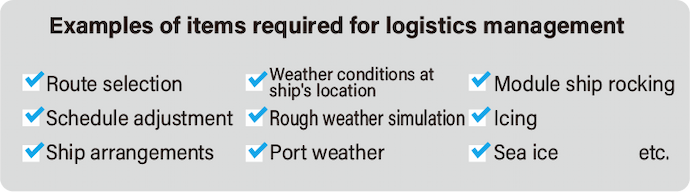
There is a modular construction method in which the modules (divided modules) are transported and assembled at the construction site.
Conventional divided modules are constructed in a box shape that includes the floor and ceiling. As a result, each divided module is tall, making it difficult to transport in areas with strict transport restrictions. In addition, the assembly work at construction sites is very difficult, so the simplest possible construction method is required.
In the divided modular construction method, we have succeeded in lowering the height of each divided module by dividing the module between the floor and ceiling. In addition, by devising a method for joining the divided modules together, we have reduced the amount of work required to assemble them at the construction sites, and this also contributes to safety. Furthermore, the fact that the divided modules to be joined share the floor and ceiling also leads to lowering the height of the module after assembly and a reduction in the amount of steel used.
- Nuclear power
- Hydrogen and Ammonia
- Oil and Gas
- Renewable energy
- Infrastructure
- Chemicals
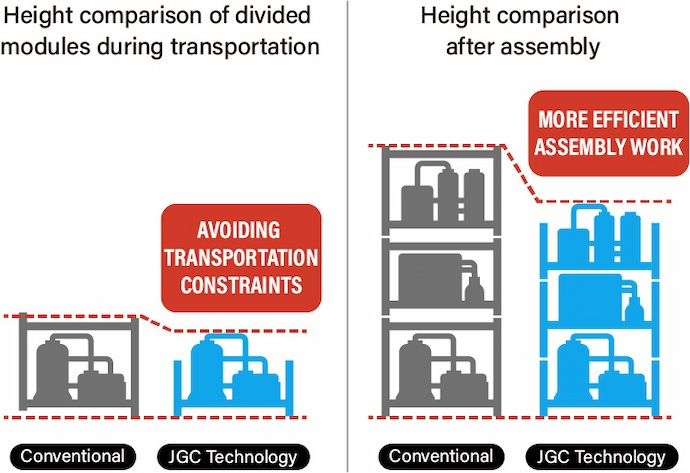
Our J・I・Module™ Concept (JGC Integrated Module ) is a technology that optimizes module layout design by taking into account factors such as budget, production volume, operating methods and site area, providing our customers with plants that have been designed with quality and safety in mind.
Modules contain hundreds to thousands of various components, such as piping, electrical and instrumentation and other types of equipment. Multiple components are integrated into a single module according to the function of each module. Then, by combining multiple modules, a complete plant can be built.
By arranging the components of the piping and equipment in a high-density configuration, each module can be made more compact. Furthermore, by arranging the modules in a high-density layout, the overall site area of the plant can be reduced.We comprehensively evaluate these benefits from all perspectives and derive the optimal solution from a vast number of combinations to propose to our customers.
- Nuclear power
- Hydrogen and Ammonia
- Oil and Gas
- Renewable energy
- Infrastructure
- Chemicals
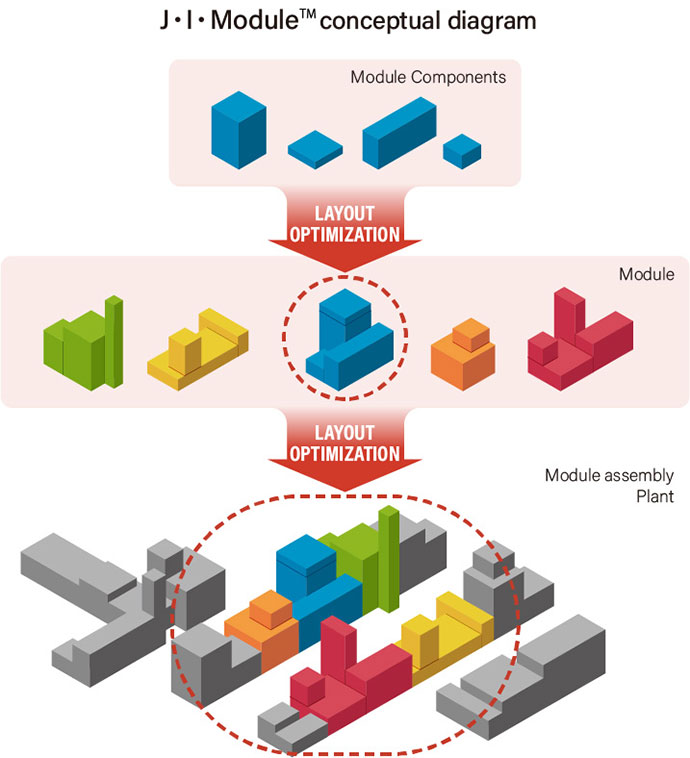
Floating facilities that operate at sea need to be stable and resistant to swaying. For this reason, it is important to design the modules mounted on the floating structure to be as low as possible, and thus lower the center of gravity.
However, with the conventional design of two rows of tanks, the tanks are located under the floor of the module, so sufficient height is required for maintenance around the tanks. As a result, the floor of the module in the conventional designs was raised, making the entire facility taller.
Therefore, we made the tank a single array and moved the space required for maintenance to the center of the module. Furthermore, by making improvements to the design of the pipe rack, it has been possible to lower the pipe rack in the center of the hull and the floor of the equipment module on the side of the hull, thereby achieving a lower level of floating equipment.
- Nuclear power
- Hydrogen and Ammonia
- Oil and Gas
- Renewable energy
- Infrastructure
- Chemicals
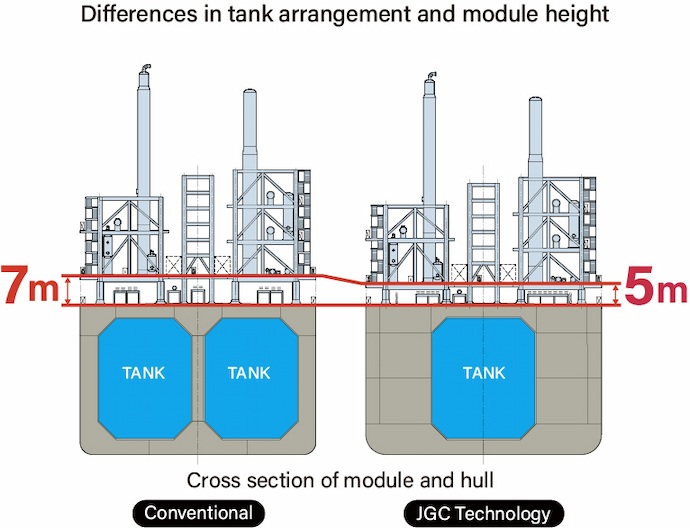
The properties of natural gas produced from natural gas fields on the seabed vary depending on the gas fields.
The construction period for an FLNG*, which is tailored to the properties of the diverse natural gas, is long, and there is the issue that it is difficult to reuse it at other natural gas fields.
To address this issue, we have come up with an FLNG concept that features standardized liquefaction modules and reconfigurable pre-treatment modules. This makes it possible to reuse the FLNG in different natural gas fields simply by reconfiguring the pretreatment module.
Our FLNG concept is an innovative idea that brings together the know-how that our group has cultivated.
*FLNG: Floating LNG, floating liquefied natural gas production, storage and offloading facility
- Oil and Gas
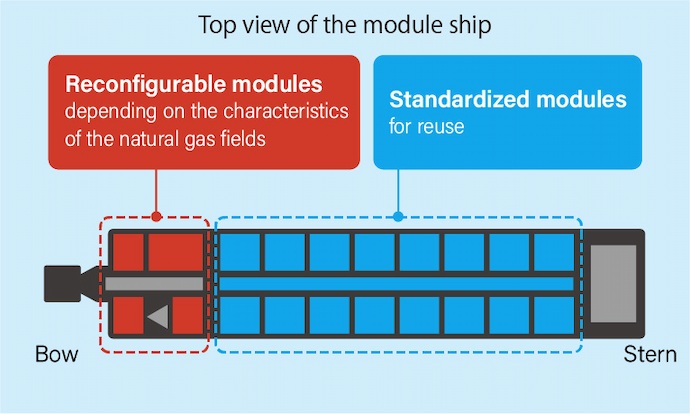
What is the modular construction method?
This is a construction method in which "modules" containing steel frames, piping, equipment, etc. are manufactured at a location separate from the plant construction site, and are then transported to the site and installed. This is an alternative to the more traditional stick-build construction method for building plants in which the plant is assembled from scratch after the necessary construction materials have been transported separately to the construction site.
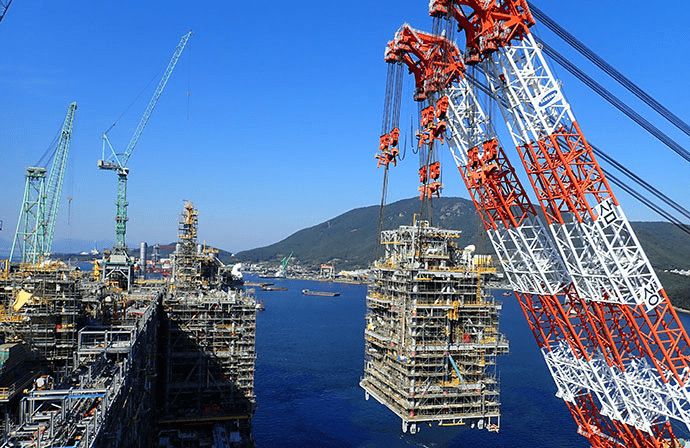
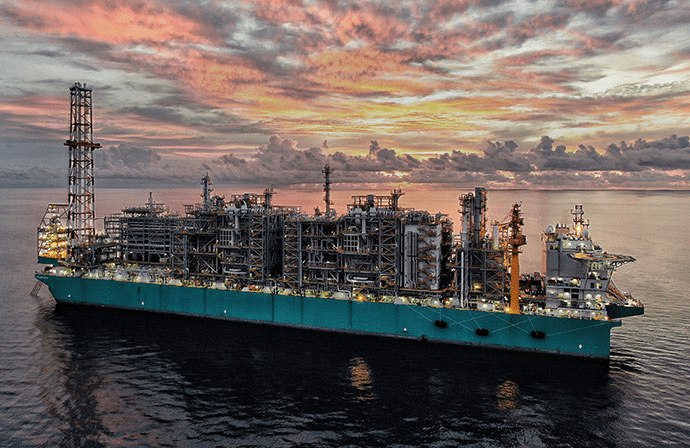
Merits of modular construction methods
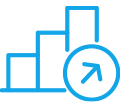
Since most of the work is carried out in the module yard, the amount of work required on the construction site can be significantly reduced.
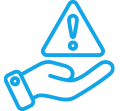
We reduce risks arising from the on-site environment in each country and region, such as responding to unpredictable weather conditions and securing workers.
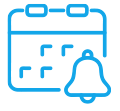
Period
Since module production and foundation work at the construction site can be carried out simultaneously, the construction period can be shortened compared to conventional stick-build methods.
Cases where modular construction is suitable
In choosing the most suitable construction method for a facility it is important to make a comprehensive decision based on all of the aspects involved, including cost and schedule for plant construction. The modular construction method involves processes that are not part of the stick-build method, such as selecting a module manufacturing yard and arranging for the transport of modules, and it is essential to coordinate and manage various restrictions. In general, modular construction is suitable for the following types of cases.
- Areas where the construction period is limited due to temperature or climate (e.g. cold regions, etc.)
- Areas where it is difficult to secure workers
- Areas with strict security conditions
Extensive experience
We have extensive experience in modular construction methods in fields such as LNG (liquefied natural gas), FLNG (floating LNG), and oil refining. In addition to our work with LNG facilities, we also have module construction technology and know-how that can be applied to a wide range of fields, including hydrogen, ammonia, renewable energy, and nuclear power. This enables us to reliably maintain high-quality as we carry out even those projects subject to severe conditions.
Module construction method FEED*/EPC* track record
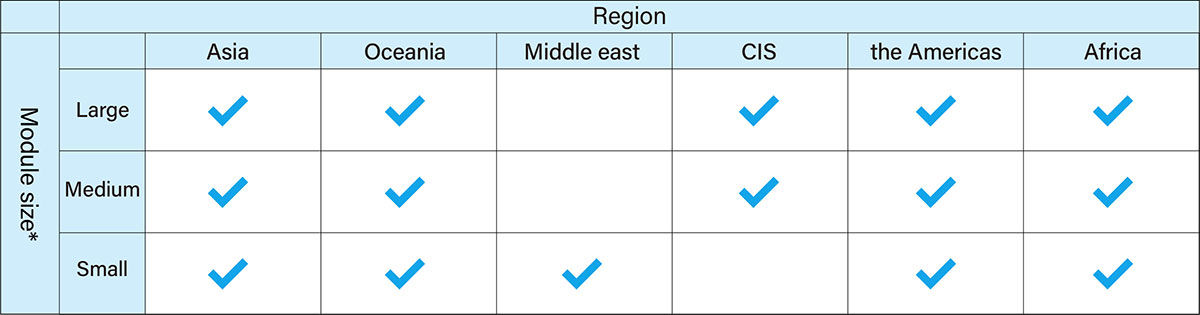
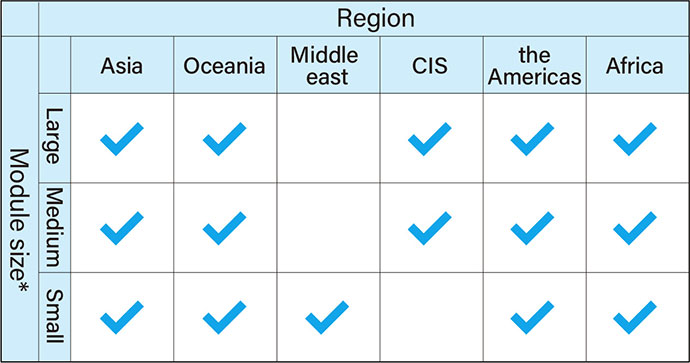
- *For each module,Large: 3000 tons or more, Medium: 1000-3000 tons, Small: less than 1000 tons
- *FEED: Front End Engineering Design, the basic design of the plant carried out in accordance with the business facility plan (plant capacity, equipment configuration, etc.), the preliminary stage of EPC
- *EPC: an acronym for Engineering, Procurement, and Construction