Highly Efficient Post Weld Heat Treatment (PWHT) Technology
Piping installation involves tens of thousands of PWHT points in a large plant, and dozens to hundreds of points even in a small maintenance project-a fact that means the impact of PWHT on a piping construction schedule can be considerable. This highly efficient PWHT technology using induction heating is a time saving technique that enables a far higher heat-up rate (1,000 degrees C/Hr) than conventional PWHT with an electric resistance heating element.
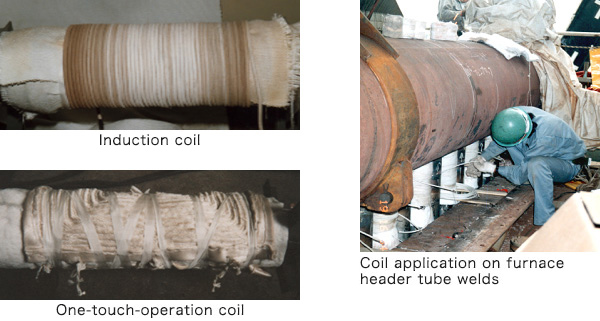
Features
Heat-up Method | Rate (degree C/hr) |
Efficiencies |
---|---|---|
Conventional electric resistance heating | 200 | 1 step/night |
Induction heating | More than 1,000 | 2 steps/night |
- Wide and uniform heated zone
Wide enough to cover ASME-specified uniform heated zone at PWHT - Highly accurate temperature control
Inverter-controlled power source enables accurate heat-up/hold/cool-down steps - High level of safety
Differ from annealing with an electric resistance heating element, a non-heat-generating induction coil assures a high level of safety - Easy installation
One-touch-operation coil (a built-in coil sheet to be placed around piping) enables simple fixing and removal as compared with induction coil winding around piping
Applications
- Piping construction in general, furnace tubes
Experience
Plant/Piping | Materials | No. of Joints |
---|---|---|
Amine Plant | Carbon Steel | 200 |
Gas Plant | Carbon Steel | 800 |
CCR Plat. | 9Cr-1Mo+Incoloy800 | 250 |
HDS/CCR | Carbon Steel,9Cr-1Mo | 800 |
CCR Plat. | 1-1/4Cr-1/2Mo | 50 |
CCR Plat. | 9Cr-1Mo | 500 |
Gas Plant | Carbon Steel | 160 |
Gas Plant | Carbon Steel | 850 |
Energy Transition - O&M/Other Services
- Consulting Service for Reliable Plant Maintenance
- Highly Efficient Post Weld Heat Treatment (PWHT) Technology
- Materials Selection for Plant Facilities
- Improvement of Maintenance Strategy to Corrosion Damages; Investigation of the Root Causes and Countermeasures
- Flow Simulation Technology
- Dry De-SOx/De-NOx System